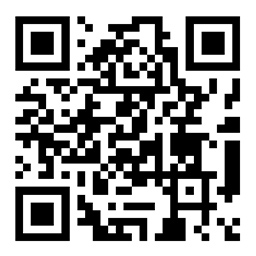
压力容器封头坯料和模具的设计
封头心部减薄使裙座底面到封头底部的高度增大到2728mm无法满足设计要求。封头成形影响因素分析影响封头成形的因素有很多,包括坯料形状、加工速度、加工温度、模具形状、模具间隙、摩擦系数等。这里分析坯料形状和模具尺寸对裙座位置的影响。
下模圆角半径的改变对锻件心部减薄量影响不大,对锻件总高度影响很显著。采用较大的下模圆角半径,有利于坯料板下落,可以减少在成形后期封头侧面的拉薄量,避免裙座底面的高度过大。采用较小的下模圆角半径,增加了成形后期对封头壁的拉薄量,有助于减小封头内壁与上模的间隙,但容易使裙座底面的高度过大。
坯料和模具1设计可以采用如下的步骤。
1)用等面积展开法,坯料板半径和预成形凸台的初步尺寸;选择合适的下模圆角半径和模具间隙。
2)用数值模拟方法,坯料板心部的减薄量和锻件的总高度;根据减薄量将预成形凸台的位置向坯料心部移动。
3)调整预成形凸台的尺寸,使成形后的裙座位置满足设计要求。
4)根据封头内壁间隙的尺寸,调整上模半径和坯料板厚度。根据数值模拟结果设计了带裙座封头的成形工艺,并进行了全尺寸试验。试验结果证明:基于ANSYS软件的封头成形模拟模块,可以准确地预测出封头锻件的形状和成形缺陷;如果坯料板不采用过渡圆角,会在裙座底面转角处产生裂纹。
数值模拟结果表明,带裙座封头的热成形具有两个显著的特征:坯料心部出现明显的局部减薄,导致裙座底面距离封头底部的高度过大;裙座部分不容易弯曲,在封头内壁与上模之间形成间隙。在设计成形工艺时,需要考虑坯料板形状和模具尺寸对封头形状的影响。数值模拟方法为坯料和模具设计提供了的依据,在不同尺寸整体封头的成形工艺设计中了成功的应用。